PRODUCTS
Moulds and retorts for industrial heat treatment furnaces
Customized solutions that withstand high temperatures, corrosive atmospheres and extreme conditions in industrial furnaces.
Contact us now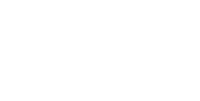
Specialists in the design and manufacture of high quality muffles and retorts.
We are a leading manufacturer of muffles and retorts for industrial furnaces, designed to withstand the most demanding conditions in heat treatment processes. With 60 years of experience, we offer customized solutions that guarantee optimum performance and exceptional durability.
Contact with us
If you are looking for superior quality muffles and retorts for your industrial furnaces, look no further. Write to us and our team will contact you to offer you a customized solution.
I want more informationWe manufacture our muffles and retorts with alloys resistant to extreme heat and oxidation, ensuring durability and optimum performance in any industrial environment.
Moulds and retorts designed for demanding environments
We offer refractory steel muffles and retorts designed to withstand high temperatures, corrosive environments and demanding industrial processes. Our products are ideal for applications such as:
- Heat treatment (case hardening, tempering, quenching, etc.).
- Sintering and bright annealing.
- Processes with active atmospheres inside the furnace.
Our Steel Alloys: Strength and Durability for Industrial Boilermaking
Discover our steel alloys, specially designed to withstand high temperatures and corrosive environments, ensuring optimum performance in demanding industrial applications.
High temperature resistant alloys
- ALLOY 80-20: Ideal for the manufacture of electrical resistors, withstands temperatures up to 1,150ºC.
- ALLOY 600: Offers high mechanical performance and oxidation resistance up to 1,150ºC. Uses: construction of furnace elements, reactor vessels and heat exchangers.
- ALLOY 601: Designed for temperatures above 1,000ºC thanks to its chromium-aluminum protective layer. Applications: Furnace parts, muffles and heat treatment tools.
- ALLOY DS: Excellent performance in oxidizing atmospheres up to 1,000ºC and hot-cold thermal processes. Uses: Furnace spare parts and heat treatment tools.
- ALLOY 800: Resistant to oxidizing and reducing atmospheres. Does not form “sigma phase”, ideal for high temperature process equipment.
- AISI-310: High resistance to oxidation up to 1,100ºC. Uses: Furnace refractories, heat treatment tools and refractory wire cloth.
Corrosion resistant alloys
- ALLOY 825: Superior corrosion resistance in contact with sulfuric and phosphoric acids.
- AISI-316L: Improves resistance to intergranular corrosion due to its low carbon content. Uses: exchangers and condensers.
- AISI-316: Resists phosphoric acid attacks up to 40ºC, hydrochloric acid diluted to 1% at 20ºC, and certain concentrations of sulfuric acid at 20ºC. Applications: naval, chemical and textile industry.
- AISI-304L: Improves the properties of AISI-304 against intergranular corrosion.
- AISI-304: Resistente a los ataques corrosivos más comunes, mantiene excelentes características mecánicas incluso a temperaturas criogénicas.
Why choose us?
Proven experience
With 60 years in the industry, we are a benchmark in the manufacture of industrial boilermaking components. We work closely with our customers to offer customized solutions that meet the highest quality standards.
Total customization
If you do not have construction drawings, we use reverse engineering to recreate the exact dimensions and build muffles or retorts that perfectly fit your needs.
Continuous innovation
Our team of welders implements advanced technologies, guaranteeing precision finishes and greater structural strength.